HISTORY OF MIG (GMAW) WELDING
continued-- Page 2
SHORT AC
EXPANDS THE PROCESS USE
“Spay Transfer” (as defined in the early
patents) when practiced for out-of-position welding, required wires as small as 0.020
diameter. Puddle control and weld penetration were problems with this
approach not to mention wire feeding difficulties. This limited the use of the process.
The short circuiting, or “Short Arc” mode of metal transfer
was developed to: 1) allow welding with more practically sized wires, like
0.035 inch diameter, 2) maintain puddle control and 3) reduce spatter by having
the arc extinguish at a high frequency.
A colleague
from the Linde Division of UCC Labs, Gus Manz (who has over 30 patents in the welding field)
filed Patent Number 3,054,884 in September 1960 that was assigned to Linde.
It defines how and why a MIG arc
behaves as it does. He defines a way to optimize the arc and weld performance
by controlling the power supply slope and inductance, particularly for welding
in the short circuiting mode. See photograph left of this power supply in use,
called the Linde SVI-300.
Manz in patent number 3,051,020 filed in August of 1962 and
assigned to Linde, describes circuits to control this short
circuiting. Subsequent patents, 3,051,829; 3,250,894 and 3,275,797 describe
refinements to this process.
|
Shielding
gas mixtures also aided the production of quality short circuit welding.
Al Lesnewich et al from Airco filed patent 3,496,323 in December of 1965 which
defined a 40 to 50% Argon, 1 to 15% CO2 and 1 to 15% Helium mixture for short
circuit welding.
With the advent of product designs making “Short Arc”
welding easy and economical to use, the MIG process gained much broader acceptance.
It could now be used for all position welding. A “One Knob” welder was
defined by Manz in Patent Number 3,125,671 applied for in May of 1962 and
assigned to Linde. This was the first easy to use device for the welder
who was familiar with welding with stick electrode. It had the “One Knob”
he new how to adjust, heat! Turn it clockwise and the “heat” increases. You can see from this old
photo there were no other knobs on the feeder or power supply. These
controls were linked mechanically within the welder! When the outside
"Heat Knob" was tuned a properly sized pulley and belt arrangement tuned the
wire feed sped potentiometer the proper amount. (Even with the elaborate electronics
we have today where making a system of this type would be much easier, everyone
insists on putting on more controls than needed! Maybe someone will produce a
“One Knob” welder again!)
|
FLUX CORED WIRE
Although we will not
attempt to cover all the innovations in welding materials for MIG welding, the
introduction of Cored Wire, both flux and metal cored, significantly increased
the use of the MIG process and should be recognized. As early as September 1918, E. H. Jones
of Great Britain filed a patent, number 1,387,157 for a product which put flux
into a metal sheath (photo left.)
|
Bernard filed on March 18, 1953 what most consider the
basic Patent for MIG Cored Wire, Patent Number
2,785,285 which was assigned to NCG. No mention is made of the need for a
shielding gas or the ability to have no shielding gas although mention is made
in the Specification of incorporating; " a gas “absorptive material.”
Later in the 50’s additional Patents related to the chemistry of the wires and
fluxes were also issued to Bernard. NCG introduced Flux Cored Wire products that
utilized CO2 for shielding. About the same time, in the late 1950’s, Lincoln
Electric introduced a Flux Cored Wire where an external shielding gas was not
need. Their trade name was InnershieldTM
which remains today.
Compared to the early self shielding flux cored wires, some of today's products
can produce welds with high notch toughness and are resistant to brittle
fracture. Self shielded flux cored wires have higher fume and spatter
than gas shielded wires but
can tolerate winds of about 20 mph where gas shielding processes are limited
in use to about 5 mph. They can be often be employed without the
need for wind breaks when welding out-of-doors. |
Side Bar
An interesting
anecdote about the development of self shielding cored wire mentions a reported
comment by Jim Lincoln, who remained as the head of the company bearing his
name until his death in 1965 at age 82.
One
of their research engineers reportedly showed him a flux cored wire he
developed that used CO2 gas shielding. Jim Lincoln (who had
fought the major gas companies promoting oxyacetylene "gas welding" over
"electric welding" much of his
carrier) reportedly said something like, "If I wanted you to use gas shielding I would have
asked for that - go back to the drawing board!”
Reinforcing
the companies dedication not to support anything that could assist their gas
supplier competitors, is Lincoln’s first compact MIG welding machine
designed for Innershield welding with their gasless wire. When lifting the wire access door, a label
inside stated something to the effect, “This machine is not designed to
be used with gas shielded wire, you do so at your own risk!"
Lincoln also
refused to label their 1st small diameter solid wire as meeting AWS
Specifications for MIG welding! William Irrgang heading the company at
the time, was 58 years old when he became President
and followed Jim Lincoln's business philosophies. The small diameter MIG
sold wire they sold was labeled with a Submerged Arc Specification, AWS
SFA5.17; EM13K. It is likely little, if any, of the 0.035/0.045 inch
diameter wire was every sold for use with the submerged arc process! It is the same
alloy as the MIG wire specification AWS SFA5.18;
ER70S-3, however they did not have to endorse the use of shielding gas by
reporting the wire qualification test was made with gas!
Finally, strengthening the centrally lead, focused business approach is an incident I was told
by a Lincoln salesperson many years ago while a guest speaker at
his local AWS Section Meeting. Bill Irrgang and Ted Willis (then 2nd
in command at Lincoln) were at a sales meeting and someone mentioned the
word MIG when asking a question. The 2nd time MIG was mentioned Mr.
Willis reportedly stood up and the room was silent (he was very tall.)
He stated that Mr. Irrgang indicated anyone who feels the urge to say the
word MIG again can leave the room now!
JF Lincoln created is a very successful welding company that has
many unique and employee
supportive business practices. The company has successfully changed in
modern times from some of the older practices mentioned above but it is of
historical interest to see the business success achieved and Lincoln's
influence on the history of welding with these centrally driven,
focused philosophies.
See
Lincoln
Info
The unique management techniques employed by Jim Lincoln had
an influence on the development of welding history. A summary of some key points in his business book(s) and
some of my direct experiences related to the company is available as a PDF
download. The similarities to the management techniques employed by Henry Ford and Fred Taylor's
work are included.
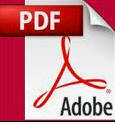
CLICK to Download PDF
Lincoln Electric received a lot of positive press from Harvard Business Review, etc. Some came from what was a unique business philosophy of focusing on being low cost producer, making the same products cheaper and lowering prices. But most came from paying hourly workers very high bonuses that in years past was 100% of earned salary and in the mid 1970's for some exceeded $100,000 total compensation. They also guaranteed a 30-hour work week in tough economic times.
However, that very ridged philosophy had flaws, and some are only coming to light in a Book from a former Lincoln CEO, Don Hastings! This paper gives an insight into how we competed with this low-cost producer, often using what the founder, JF Lincoln advised in his management books! Hope you find a fun read.
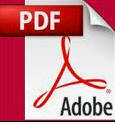
Click to Download PDF
|
UNIONARC
Another
innovative process variant was introduced by Linde Division of UCC known as Unionarc.
Harry Kennedy, who had the
basic Submerged Arc patents, in
September of 1941, filed Patent number 2,326,865 which was assigned to the
Linde. As mentioned under the History of Submerged Arc, he was receiving a
substantial royalty for the use of that process. He claims in that patent the
use of 10 to 20% ferrous metal in a flux to make it cling to a DC electrode.
That process was refined and Patent Number 2,947,847 filed January 1955 and was
issued to Craig, Rockefeller, Stanchus and Davis, assigned to the Linde Division
of UCC. [I
knew the fist three well. Crag and Stanchus worked in the Linde Division
of UCC Labs as
did I. Rockefeller was the General Manager of the Linde Division of UCC Welding Department
when I joined the Lab. Now I understand why he came to see me weld with
his "Bottle
Torch” some years later! The "bottle torch" was an interesting simple
method of applying Unionarc. Instead of a complex device needed to feed
the flux to the torch a small plastic bottle of flux was placed on the torch and
feed the proper amount of flux by gravity. It worked! ] As noted in the figure from their patent (left), a
magnetic flux was transported by CO2 from a pressure container to the
torch. The torch also had a conventional solid wire going through the contact tip
(usually 3/32) and the magnetic flux clung to it as it exited the
shielding gas cup. It looked like a "hairy stick electrode!" For a variety of
reasons the process never caught on.
|
Page 1
2 3
(4 last)
Have a Welder?
Improve Weld Starts and Have Shielding Gas Cylinder Last at Least Twice as
Long!
Note: Our Patented
GSS
is Not Available in "Stores"
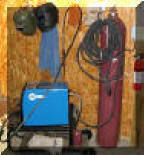
A home shop fabricator
in Georgia with a Miller TM 175 amp welder
purchased a 50 foot Gas Saver System ( GSSTM
) so he could use a larger cylinder
and mount it on the wall of his shop. He wrote:
"The system works great.
Thanks for the professional service and
a great product."
Click To See His Home Shop
A Professional
Street Rod Builder Had This to Say:
With their standard MIG welder gas delivery hose the peak shielding flow at
weld start was measured at 150 CFH. That caused air to be sucked into the
gas stream causing poor weld starts. With the
GSS replacing their existing hose, the peak flow surge at the
weld start was about 50 CFH. Total gas use was cut in half.
Kyle Bond, President, quickly saw the improvement achieved in weld start
quality as a significant advantage! Kyle, an excellent automotive painter,
was well aware of the effects of gas surge caused by pressure buildup in the
delivery hose when stopped. He has to deal with the visible effects in the
air hose lines on the spray gun in his paint booth! The paint surge is
visible and creates defects unless the gun is triggered off the part being
painted! We can’t do that with our MIG gun!
GAS SAVER SYSTEM (GSS TM)
PURCHASE INFORMATION
|
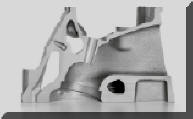
MIG Gas Delivery and the Small Block Chevy Evolved in a Similar
Way and Time!
Both had Advances and
Setbacks Before
They Were Optimized!
Click
for a PDF Report on the Similarities |

Free Technical Paper, "MIG
SHIELDING GAS
CONTROL"
CLICK ICON for PDF DOWNLOAD |
"WARNING:
"Weld
Safely" |
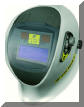 |
▲HOME
►CONSULTING
SERVICES
|