The
Basic's of
Welding 4130 Chrome Moly (Chromoly) Steel are Presented
on This Web Page
For other
4130 welding info
Click
TECHNICAL & METALLURGICAL DETAILS
Click
WELD COOLING RATE EQUATIONS
Click WELDING HEAT TREATED
4130 CHROME MOLY
Click
METALLURGICAL DEFINITIONS
Click "How To Pronounce" CHROME MOLY
Click
WELDING A BETTER STEEL; HY 130
Click
DEFINING "EFFECTIVE HEAT INPUT"
CLICK to See Side Bar Below Regarding the
Strength of Welds Made with ER70S-2 versus ER80S-D2
|
The Editor of the American Welding Societies Monthly Journal Asked Me To Write and Article on Motorsports Welding for the March 2018 Issue.
This is a PDF of what was published. It compares differences in NHRA with NASCAR chassis construction. Where NHRA top classes use high strength 4130 tubing, NASCAR belives in a "Bend Before Break" design. They specify mild steel tubing and the min wall thickness that can be used!
CLICK PDF ICON RIGHT or pic to Download a PDF. |
Our patented GSS provides better quality weld starts by reducing shielding gas turbulence. For short welds, excess turbulence can last for much of the weld. The GSS cuts gas waste using a small ID, heavy wall thickness hose incorporating a peak flow rate limiting restrictor. Over 10,000 are in use.
Check out our FB3 & FB4 GSS models.
Alert !!
Argon Prices tripled in the Past Several Years!
Air Products announced Argon price increases of 20% in three consecutive years; 2017, 2018, 2019 and 35% in 2020!!
A major producer of Cryogenic Tanks and a leading Airplane Builder have purchased over 300 GSS's for their TIG Welders to improve weld start quality and cut gas use 30 to 40% .
Video-Welding 4130
CrMoly |
4130 was widely used in WWII airplanes! It was welded with oxyacetylene as TIG welding had just been invented! With oxyacetylene the material is being preheated and cooling is slow so the relatively high carbon 4130 was considered very weldable. With TIG or MIG there is is usually no preheat used and cooling is very rapid leading to possible hard and brittle welds without employing precautions.
Of interest, in WWII about 40% of the workforce were women. This is a picture from War Archives is of Ann Rosner oxyacetylene welding an aircraft supercharger duct at Ford's Willow Run plant.
When writing "Advanced Automotive Welding" for CarTech I talked with Gene Golliet about his welding of 4130 aircraft tubing in shops in Southern California during the War. Some experimental aircraft still use and prefer that welding process.
|
Welding 4130 Chrome Moly Steel for Race Cars
During
the WW II era 4130 high strength steel was used for some aircraft components. At
that time
oxy-acetylene was the welding process of choice for many of these items. The preheat and slow cooling
inherent with that process made welding the nominal 0.30 carbon steel
relatively straight forward (assuming one could oxyacetylene weld!). However with more modern welding process like TIG and
MIG, the cooling rates can be much faster and care must be taken to avoid
forming high hardness and brittle Martensite on cooling transformation. On heavier
sections preheat and post weld heat treatment should be used. With the
proper post weld heat treatment strengths of 200,000 psi can be achieved with
reasonable toughness by tempering the Martensite that forms in the heat treating
process. However when welding race car tubing, preheat is not often used
nor are the parts post weld heat treated.
Most of the tubing used
for race car construction is referred to as normalized. This refers to the
heat treatment and cooling rate the tubing was subjected to in manufacture.
Most normalized tubing will range in tensile strength from 95,000 to 110,000
psi. This can be welded with the proper filler metals to achieve similar
strengths. Although there are more weldable grades of steel (those with
lower carbon content from 0.06 to 0.15) in the 100,000 to 115,000 psi
tensile strength range readily available for plate and sheet, 4130 remains a
commonly used grade for tubing. Just be sure to take the precautions noted
when welding.
The following is extracted from an article I wrote for the American Welding
Societies technical journal called "The Welding Journal". It has
additional information to that presented in the publication. You can see the article in the 2003 April issue of the AWS Welding Journal:
|
PROPER FILLER METAL CHOICE FOR WELDING 4130
In the mid
1970’s, while managing an R&D group for a leading welding shielding gas/filler metals manufacturer, a
phone call was received from a dragster chassis builder. They wanted to weld
4130 tubing and needed a filler metal suggestion. Being a “car buff,” a
number of alternatives were considered to provide the optimum solution. After
careful review of their requirements and desired welding practices, the solution
was defined. They were welding 4130 normalized tubing, it would not be heat
treated after welding, preheat was not desirable and most of the weld joints
were intersecting tubes that required fillet welds. The best filler material to
use was a low carbon alloy now called ESAB Spoolarc 65 (meeting an American
Welding Society (AWS) ER70S-2 specification). The main objective is to produce
porosity and crack free weld deposits. This welding alloy has a very low carbon
content, nominally 0.06, which can handle dilution into the relatively high (in
terms of weld metal), 0.30 carbon in the 4130. The resulting diluted weld
deposit has a tensile strength of approximately 590 to 620 MPa ( 85,000 to
90,000 psi.) The actual strength will depend on the amount of dilution with the
4130, weld bead size and material thickness. This is usually an under match for
the 4130 tubing which could have a 760 to 800 MPa (100,000
to 115,000 psi) tensile strength depending on how the material was processed.
[Added Note: some normalized 4130 tubing may be only have a 90,000 psi
tensile strength, it depends on the manufacturer] However, if extra joint strength is required, a slightly larger fillet size or
gussets can be employed. In addition, this welding wire contains small amounts
of aluminum, titanium and zirconium. Although these elements were initially
added to handle welding over mill scale, they also contribute to a less fluid
weld puddle. The benefit to the welder is, it is easier to make out of position
welds. Note, it is suggested all welding on 4130 be performed on ground
surfaces free of oil or grease (to keep the hydrogen levels as low as possible).
Several years after making this
suggestion, when looking at a catalog from the dragster chassis
manufacturer, it was interesting to note they were advertising their use of the
ER70S-2 filler metal for their 4130 welding. In fact, they were offering it for
sale for those customers purchasing frame parts and doing their own welding!
The Internet was searched to
see what current recommendations were being made for joining 4130 tubing.
Several hundred sites were found that recommend the ER70S-2 welding rod/wire alloy.
It was the predominant recommendation. Typical of the Internet however, there
were many improper descriptions of why this alloy should be used and several
incorrect recommendations.
Need a higher
strength deposit? If a higher strength weld is required for perhaps a butt weld
that cannot be reinforced, strengthened with a gusset, or put in a less
critically stressed area, there are possible solutions. The use of Spoolarc 83, which contains 0.50 Moly, will provide a weld deposit with higher
strength. When diluted into the 4130 base material a weld tensile level of 760
to 800 MPa (110,000 to 115,000 psi) can be achieved. If this higher strength
welding wire is employed, a minimum preheat of 65 degrees C (150 degrees F) is
suggested. Weld strength can increase to a level slightly higher
than the normalized 4130 with Spoolarc 83 (AWS ER 80D-2). Do not use an austenitic
stainless steel such as an ER308L, (which is recommended on some Internet
sites). Diluting this or similar austenitic stainless alloys with 4130 can lead
to cracks. Also, consider that providing a higher strength weld deposit cannot
compensate for the reduction in strength that will occur in the parent metal
immediately next to the weld deposit.
For Parts to
be "Heat Treated" (meaning carefully raising the part to 1600 F; Quenching in
water; then Reheating precisely to 1000 F; then Slow Cooling) After Welding:
Note: modified with additional information obtained since writing this article.
Click to See Detailed Explanation:)
If the part is to be used for
potentially high impact, structural applications and will be
heat-treated after welding, a matching chemistry or matching hardenability filler metal to the 4130 should be employed.
This may be a filler metal with somewhat lower carbon but increased moly,
chrome, manganese etc. Because of the relatively high
carbon, a minimum of 200 degrees C, (400 degrees F) preheat and very slow
cooling after welding should be used to avoid cracking. Heat treating
after welding refers to the finished welded part being heated to 870 degrees C (1600 degrees F), quenched in oil or water then
tempered back to say 540 degrees C (1000 degrees F). A complex cycle, but
this will result in a tensile strength of approximately 1035 MPa (150,000 psi).
Since the weld is the same chemistry as the base material, it and the
heat affected zone will have the similar properties as the base material when
heat-treated. All critical welds of this type should be inspected for internal
soundness to assure they are free from cracks.
|
End Of Abstracted Article
OTHER PROBLEMS ENCOUNTERED
In addition to the filler metal selection issues mentioned, some additional
cautions should be followed. Many fabricators use TIG
welding
and make very small, concave fillet welds. There seems to be a
feeling that the smaller the better. This raises several concerns.
First there is little filler metal used to make these very small welds.
Therefore the weld consists mostly of the high (by welding standards) carbon
from the 4130 base material. This can cause cracking since there is no preheat
or postweld heat treatment being used. Also cooling rates for these small welds,
especially when using TIG, can be quite high. Therefore one suggestion I
had made in the article (removed from this abstract) was that some
stainless steels filler materials could be used. This is also mentioned on
a number of Internet sites. However with these small fillet welds there is
only a small amount of stainless filler in the deposit and possibly a
significant amount of the high carbon base material. This combination can
lead to a crack sensitive deposit. It is suggested stainless filler metals
not be used for welding 4130.
Making an analysis of the resulting weld chemistry for varying amounts of filler
metal dilution creates a scary scenario at low amounts of any stainless
filler alloy. When I discussed the use of stainless filler metal making
these small fillets in 4130 tubing with a friend who is an acknowledged
"worldwide stainless welding expert," he cringed! As he said, the
suggestion that 312 stainless filler be used is based on at least 40 to 50%
filler metal diluted in the high carbon material. If you make almost an
autogenous TIG weld (no filler metal) and add just 20% of even 312 stainless you
get a Martensitic deposit. You do not obtain the desired
microstructure on which folks base their recommendation for a particular
stainless alloy rod being acceptable. I have had race car fabricators say
they like to use stainless filler because it makes the weld stand out and look
good on unpainted frames they sell! Not a good reason since it could also
contain cracks!
|
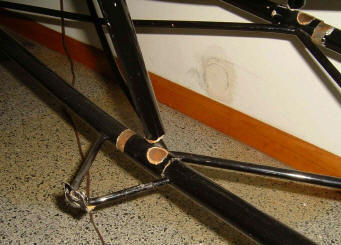
With only small additions of these filler alloys to the weld deposit there
is a high percentage admixture of 4130. In these very small deposits
this can create a crack sensitive metallurgical structure. In fact for
these small welds the use of ER70S-2 becomes even more of a preferred
suggestion.
ER70S-2 with its low carbon and leaner Manganese and Silicon alloy than some
other of the rods/wires often recommended as usable such as ER70S-6, creates
less of a dilution problem.
Small cracks and the presence of a brittle Martensitic structure in
these welds can lead to failure or can cause a brittle fracture when
subjected to a crash. See the welds in the photo of the dragster
chassis. I don't know what filler wire was used to weld these joints,
what little there was, but the fillets are very small. It
does not appear very much if any bending took place in the structure before they failed!
|
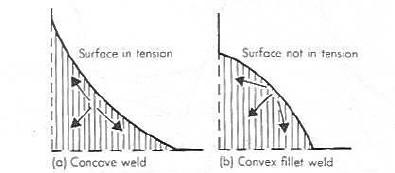
Another problem created with small concave fillet welds is when they cool the
surface is put in tension. This makes it susceptible to cracks especially near
the toe of the weld where it is very thin. (Sketches from article by Omar
Blodgett)
Bottom line is use larger flat fillets to assure less dilution with
the 4130 and a less crack sensitive shape. |
Side Bar
Had an interesting
conversation with two folks who have extensive experience welding 4130
tubing for race cars. One said his company was asked to help a
large racecar team solve welding problems. He found they were welding
with a special stainless rod "Super Missile Weld" (a 312 stainless steel rod with a fancy name.) Because of
the small TIG fillet welds they were making with very little added filler
rod, they were not getting an austenitic stainless steel weld deposit
because of excess dilution with the base material. Instead they were getting
a high chrome, brittle ferritic deposit! He took in some carbon steel
rod (the one we suggest, ER70S-2) but told them this was a "very special"
rod that would solve their problem. It did! " Just because it costs
more does not make it better!"
The other fellow who has
fabricated a number of sportsman and other drag cars and weld repaired a
number of other 4130 race cars. He saw a number of weld failures
on some chassis caused
by the very small concave fillets that had been used .
He also said some welds were made with poor, cold MIG Short Arc welds that
were not fused properly to the tubing. Both very bad welding practice.
|
STRENGTH OF ER70S-2 WELDS
The following discusses AWS TIG/MIG Filler Metal
Specifications that are often misinterpreted in Welding Forum comments:
-
The Specification that defines carbon steel wires
and rods, including ER70S-2, for MIG and TIG welding is AWS 5.18. ER80S-D2
is covered by AWS A5.28, for Welding Low Alloy Steel.
-
Both Specifications require reporting the tensile strength
from a weld made in a ¾-inch thick, mild steel weld
joint having a 45-degree V bevel angle, gapped ½-inch on a steel backing
bar. It requires many weld passes to fill this joint minimizing any
effects of the base material on weld properties. Each weld pass is
made at a defined (by the Specifications) amperage, voltage and travel
speed.
-
These welds do NOT increase in strength by mixing with
the relatively high carbon 4130 (by welding standards, it's high) as
occurs when making single pass fillet or butt welds in that material. The
weld strength in a single pass diluted weld in 4130 will be higher. The
exact strength achieved depends on the amount of rod added to the melted 4130,
joint type and thickness, welding parameters used etc.
-
Both Specifications define a minimum
tensile strength, i.e. ER70S requires a minimum
of 70,000 psi (note 1,000 psi = 1 ksi) and for ER80S - a minimum of
80 ksi. It does not say what weld strength will be produced; just the
minimum to be classified in that category. The specific
chemical range for a particular alloy (S2, S6, S7 etc) is also
specified.
-
The following data are AWS Specification weld test results
from ESAB (data is from Fig. 4-52, in my recently published book
Advanced Automotive Welding
that also discusses the implications in detail):
TIG, MIG, or Base |
Rod, Wire or (Base) |
Tensile Strength,
ksi |
Elongation,
% |
Impact Strength;
ft-lbs |
TIG Weld |
ER70S-2 |
82 |
31% |
170 |
MIG Weld |
ER70S-2 |
82 |
28% |
45 |
MIG Weld |
ER80S-D2 |
110 |
22% |
85 |
Base Material |
(Normalized 4130) |
~90 |
~25% |
~60 |
|
Bottom Line:
Even when not diluted with 4130, ER70S-2 has a tensile strength
just 9% under typical Normalized 4130. ER80S-D2 has a strength, with
no dilution with the higher carbon 4130, that is 22% higher than Normalized 4130.
Significantly higher strength weld metal than base metal may cause a
weldment, when stressed under load, to yield excessively or initiate
failures in the heat affected zone.
The elongation of Normalized 4130 (a measure of ductility) is
less than the very ductile ER70S-2 weld. The higher strength ER80S-D2 weld
has a lower elongation than the base material.
The impact properties of a TIG weld made with ER70S-2 are
excellent at 170 ft-lbs. Note, the reason TIG welds have higher impact toughness
than MIG welds made with the same alloy filler metal is discussed in the
Advanced Automotive
Welding book. |
CHECK WELD QUALITY
It is very important to check
weld quality and understand the types of defects that could be encountered.
Check your weld procedures and keep them consistent. You should make some
sample welds and bend them to destruction to assure failure occurs only after
considerable bending has taken place. Look for porosity or cracks that may
have been present in the weld. It would be a wise investment to hire the
services of an American Welding Society (AWS)
Certified Welding Inspector (CWI). There are some 25,000 registered.
In fact many of them are members of the 65,000 member AWS. They can
advise on procedures and what to check for such as small undercuts at the weld
toe of fillet welds that can lead to premature failure.
Consistently following the
proper weld procedures and knowing how to check for possible weld problems is of
major importance.
Closing Suggestion
When welding 4130 chrome moly in the
normalized condition, AWS ER70S-2 filler metal, with its low carbon content is
the proper choice. Make sufficiently large fillets and make them flat, not
concave. If the part is to be heat-treated after welding, then a
filler metal matching the 4130 chemistry should be employed. This requires
preheat and special precautions to avoid cracking.
Be sure to employ the skills of a qualified
welder who has experience welding this material. Also inspection of the
final welds by an Certified Welding Inspector (Certified by The American Welding
Society) is highly recommended.
(Welding Mild Steel Chassis's or Roll Bars? Click Here) |
Improve Weld Starts
and Save Money by Eliminating The
"Gas Blast" at MIG Weld Starts That Causes:
1)
Inferior Weld Quality and Excess Spatter
- due to the air pulled into the gas stream
2)
Shielding Gas Waste
- typically 50% of gas used
See Patented
Gas Saver System (GSS)
Solution
GSS
Works for TIG Welders with Foot Pedal or Thumb Control
|
FREE
Technical Paper Available Entitled; "MIG Shielding Gas Control and
Optimization" (or Everything You Didn't Know You Needed to Ask About
MIG Shielding Gas Control!) It Summarizes Key points in this Web Site
and numerous Technical Presentations made in US and International Welding
Conferences about the gas shielding problems and solutions. 
CLICK ICON for PDF DOWNLOAD |
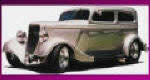
Stop
Wasting Shielding Gas!!
See YouTube Videos
Including Our Patented MIG Shielding
"Gas
Saver System" (GSS)
The
Basic's of
Welding 4130
were presented on
this page:
Click for
TECHNICAL & METALLURGICAL DETAILS
Click for
EQUATIONS
defining weld cooling rate in tubing
Click for
WELDING HEAT TREATED
4130 CHROME MOLY
Click for
METALLURGICAL DEFINITIONS
Click for
WELDING A BETTER STEEL; HY 130
|
Why MIG Gas Waste
Detailed Review of GSS
Short Overview of GSS-90 Seconds
What User Say About
GSS
Welding Race Cars
Rat Rods-Then and Now
Welding: Go Green
Engineering A
Pro Street / Street Rod
|
ONE PAGE SUMMARY
PURCHASE
PRODUCT

FREE Corvette Accessory Installation Info
Miller TM is a trademark of ITW
Corporation |
▲HOME
|